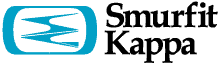
Téléchargez un PDF de l'histoire.
Groupe Smurfit Kappa
Témoignage client
En continuant, vous acceptez le traitement de vos données personnelles par GlobalVision tel que décrit dans le Politique de confidentialité.
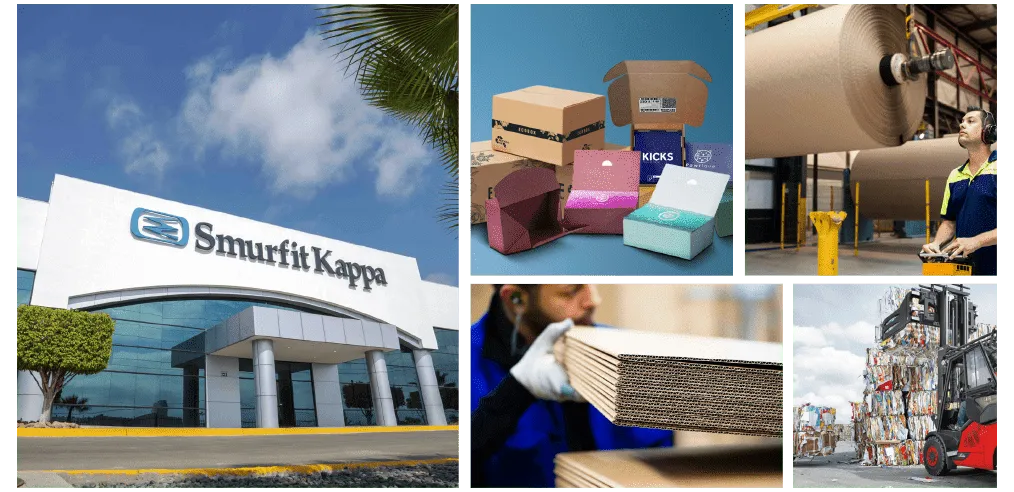
« Même avec des impressions à 100 % et une « nouvelle paire d'yeux », la procédure (manuelle) prenait beaucoup de temps et n'était malheureusement pas concluante en raison des limites humaines liées à la détection des erreurs. »
M. Van der Klis, Responsable de la préparation de l'impression graphique
GlobalVision aide Smurfit à réaliser des impressions et des emballages exempts d'erreurs
À propos du groupe Smurfit Kappa
Schtroumpfit Kappa est un membre éminent du Financial Times Stock Exchange (FTSE) 100, reconnu dans toute l'Europe comme le premier producteur d'emballages en carton ondulé et un leader mondial des emballages à base de papier. Ses activités vont au-delà de l'emballage pour inclure le papier, le recyclage et la sylviculture, fournissant un réseau de services complet et intégré.
Présent dans 36 pays d'Europe et des Amériques, Smurfit Kappa employait près de 48 000 personnes dans le monde en 2023, et générait un chiffre d'affaires impressionnant de 12,8 millions d'euros en 2022. Le siège social de la société est situé à Dublin, avec des sièges régionaux supplémentaires à Amsterdam et à Miami.
Le portefeuille innovant de solutions d'emballage en papier de Smurfit Kappa est inégalé, avec des mises à jour constantes et des développements de pointe. Ils produisent une grande variété de papiers principalement utilisés pour l'emballage, avec une capacité mondiale totale d'environ 8,3 millions de tonnes par an.
Le défi : les contrôles manuels sont sujets à l'erreur humaine
En raison de la nature hautement spécialisée de ses produits et services, le groupe Smurfit Kappa doit garantir la plus haute qualité de ses impressions et de ses emballages. Des erreurs ou des erreurs dans les fichiers ou les illustrations peuvent entraîner des rappels préjudiciables, des pertes financières ou une diminution de la fidélité et de l'intégrité de la marque, autant de problèmes qui pourraient autrement être très difficiles à corriger.
Auparavant, Smurfit Kappa MNL utilisait les contrôles visuels manuels comme principale méthode de relecture des actifs critiques. Selon M. Van Der Klis, responsable de la préparation de l'impression graphique sur leur site aux Pays-Bas, la relecture manuelle des fichiers et des illustrations était extrêmement chronophage, inefficace et sujette aux erreurs.
L'erreur humaine est l'une des causes les plus courantes d'erreurs manquées, car le cerveau a tendance à corriger les erreurs automatiquement. Cela rend la recherche manuelle des erreurs extrêmement difficile et les erreurs passent inaperçues et passent inaperçues.
Pour garantir la qualité, la précision et la cohérence de ses produits, Smurfit Kappa MNL aux Pays-Bas s'est tournée vers Vision globale comme solution à leurs problèmes d'inspection et de vérification.
« GlobalVision apporte son aide dans les opérations quotidiennes. Nous nous appuyons sur lui pour vérifier le contenu du texte, des logos et des éléments d'impression manquants. Cela nous permet de nous concentrer sur les contrôles techniques d'impression. »
M. Van der Klis, Responsable de la préparation de l'impression graphique
La solution : minimiser les erreurs et garantir la qualité grâce à l'automatisation
Selon M. Van der Klis, les fonctionnalités de GlobalVision telles que la sélection des couches, l'échelle de correspondance, l'inclusion/exclusion de pages et la prise en charge des répétitions multiples (avec rotation) ont joué un rôle déterminant dans ses processus d'inspection et de révision. En outre, la possibilité d'effectuer une vérification automatique entre l'illustration et les fichiers ajustés de différentes tailles, formats et couches sélectionnées/désélectionnées s'est révélée extrêmement utile et l'une des principales raisons pour lesquelles ils ont opté pour GlobalVision.
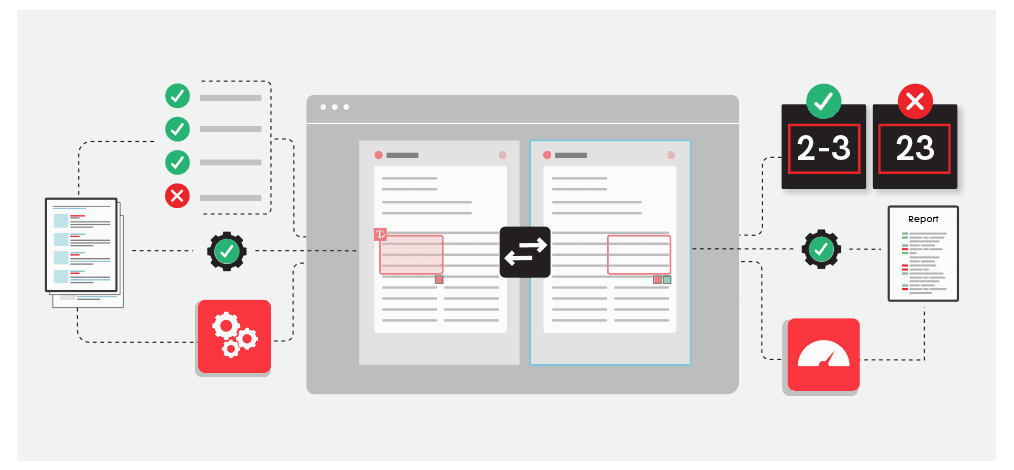
La détection manuelle de différences mineures et apparemment insignifiantes est difficile et peut entraîner des problèmes importants si elles ne sont pas détectées et corrigées immédiatement. Les fonctionnalités et les capacités de GlobalVision ont permis aux équipes de révision de Smurfit Kappa MNL non seulement d'identifier toutes les différences, mais également d'optimiser leurs inspections, leur permettant de se concentrer sur la correction et l'ajustement de leurs fichiers pour une perfection pixel par pixel.
L'association avec GlobalVision a procuré à Smurfit Kappa MNL plusieurs avantages, notamment :
- Productivité accrue
- Efficacité accrue des flux de travail
- Diminution des temps et des cycles de révision
- Diminution des erreurs
Conclusion
En mettant en œuvre Le système d'inspection de contrôle qualité de GlobalVision, Smurfit Kappa MNL a pu automatiser ses flux de travail d'inspection et de vérification et combler les lacunes connues dans ses processus de relecture.
Cela a permis de réduire considérablement le temps passé à vérifier les erreurs dans les illustrations et d'éliminer le besoin de ressources ou de personnes supplémentaires pour vérifier et relire les fichiers. Le système a également réduit le risque que les clients rejettent l'emballage en raison d'erreurs d'impression, réduisant ainsi la frustration et améliorant les relations avec les clients.
Lorsqu'on lui a demandé ce que ferait Smurfit Kappa si GlobalVision était retiré du marché, M. Van der Klis n'a pas tardé à répondre : « Cela entraînerait un sérieux revers ! » Le système fait désormais partie intégrante de leur flux de travail et son absence serait grandement ressentie.
Chez Smurfit Kappa MNL, le fait de s'appuyer sur des vérifications manuelles pour détecter des fichiers exempts d'erreurs représente un risque important qu'ils ne peuvent pas se permettre de prendre. Même avec une vision 20/20, les contrôles manuels peuvent entraîner des erreurs mineures qui peuvent entraîner des résultats néfastes. Pour éviter totalement ces scénarios, Smurfit Kappa fait de GlobalVision un élément essentiel de ses processus d'inspection et de vérification quotidiens.
« GlobalVision a réduit la frustration et réduit le risque que les clients rejettent un emballage en raison d'une erreur d'impression. »
M. Van der Klis, responsable de la préparation de l'impression graphique