
Download a PDF of the story.
Bemis Company Inc.
Customer Story
By continuing, you agree to the processing of your personal data by GlobalVision as described in the Privacy Policy.
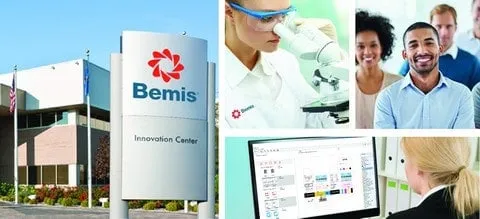
“Like any company, we would miss things. It could be anything from copying text incorrectly and misspelling a word, to nudging a logo and inadvertently dropping something off the artwork. Unfortunately, there were times when we would print something incorrectly.”
Jeff Hochhausen, Bemis Graphics
Bemis Co. Implements Esko Automation Engine with GlobalVision Proofing System to Catch Packaging File Errors
Headquartered in Neenah, Wisconsin, Bemis Company Inc. has played an influential role in the packaging industry ever since its founding in 1858. Now the largest flexible packaging company in the Americas, Bemis serves customers worldwide and their products are found in virtually every aisle of the grocery store. With 61 facilities in 12 countries worldwide, they offer unmatched size and scope. But with expansion of any company arises the issue of quality control. A company of Bemis’s footprint can easily open themselves up to oversight without a proven process in place to ensure their manufacturing capabilities remain world-class. Enter ESKO and GlobalVision.
More than brand names on the line
Missing a graphic element or printing incorrect text on packaging can be extremely costly for the printer or converter. The ultimate cost could be a product recall, with extremely expensive product costs and, more importantly, damage to the brand itself. However, the manual proofing process can be time consuming and inconsistent—and can result in a review process that can miscommunicate edits, resulting in errors. Those errors have a greater effect than ruffling the feathers of a client relationship.
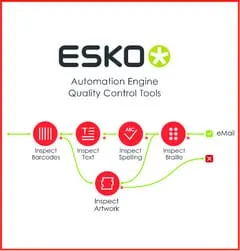
“We know that if we used this process last year, we would have caught eight errors. It is hard to catch them manually.”
Jeff Hochhausen, Bemis Graphics
Deleting complacency from the process
In their prepress department, Bemis Graphics in New London, WI originally proofed files like everyone else by using just their eyes. Though unlike software, eyes get strained, exhausted, and soon start missing crucial details. Without needing to weigh other problematic factors into the equation, Bemis decided the mistakes couldn’t continue. Eventually, the company moved to Automation Engine tools, using Viewer Compare, which places two files on top of one another and highlights the differences. It worked well, but they wanted to find an even more automated solution that would save operator time and be less error-prone.
“While we had been using Esko tools for decades, we learned about GlobalVision when we were tasked to compare printed jobs back to the proofs for details like the correct plates, proofs, color and copy. Things can get missed there,” remembers Hochhausen. “From an overall business standpoint, GlobalVision’s ScanProof, where we scan a press sample and compare it to a visual PDF, worked perfectly for us. Then we wondered, ‘Why build this feature into our workflow?’ GlobalVision had a server-based option where we could drop two files into a hot folder—the scan and the Automation Engine-generated PDF file. We were looking to automate the process to add speed. Certainly, an automated system is faster and more accurate than what a person can do… I spoke with Esko during EskoWorld and wondered if they could integrate GlobalVision tools into Automation Engine,” recollects Hochhausen. “The next year they brought us a beta solution and asked us to test it out.” The rest is history, well, recent history. Bemis has been using GlobalVision tools paired with Automation Engine together since the beginning of 2016 and they haven’t looked back since.
After years of doing things “the right way,” it’s easy for redundant steps to go unnoticed. In Bemis’s case, they could always conduct their spell checks in Adobe Illustrator, but by using that process each library in every workstation has to be changed when new words are added. “By implementing the spell check within Automation Engine, we only have one library,” comments Hochhausen. “Now, when words or ingredients are added to the library, everyone has the change instantly. We can also guarantee that our artists are running the spell check, because it is automatically triggered by Automation Engine. Before, we couldn’t be sure.” What Hochhausen can be sure of now, is that unnecessary steps have been eliminated from their company’s workflow and what’s been added is increased ROI.
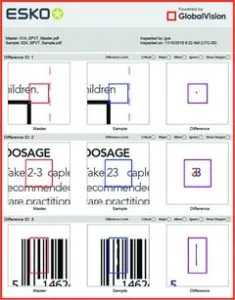
“What I like most is the speed we can get along with the confidence that nothing has changed—other than those elements that the client has requested. I would say tasks like the barcode check, alone, saves us ten minutes per job. Before we were checking the print and scanning the proof. We were walking away from the desk to scan the proof and manually check the barcode. Now it is done automatically,” adds Hochhausen. Management is very interested in the system’s ROI. “The system certainly saves time on artwork. We also hope that, once we update to Esko Software Platform 16, we will be able to collect and pull out XML data that will show us how many errors have been caught,” remarks Hochhausen. “It is easy to do with Automation Engine, Automation Engine Connect, and the MIS. That could be very valuable.”
One of the nice surprises is that Bemis has even found other ways to use GlobalVision tools. “For example, in our order entry process, we create orders like anyone else and generate a PDF file from it. If someone else touches the order and adds something unwanted, we can detect those changes in the order,” says Hochhausen. Unexpected results like these are exactly what push ESKO and GlobalVision further. It’s proof that when businesses commit to partnerships, something more valuable than money arises; knowledge.