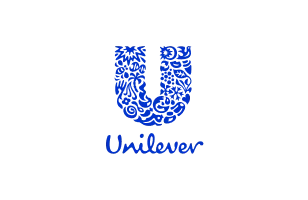
Download a PDF of the story.
Unilever
Customer Story
By continuing, you agree to the processing of your personal data by GlobalVision as described in the Privacy Policy.
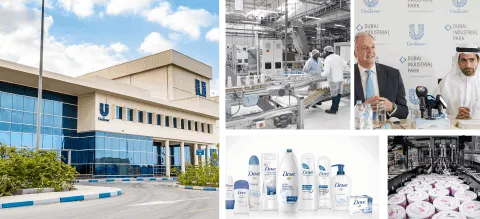
“Overall, the team is able to save between 10-15 minutes per label when proofreading with GlobalVision.”
– Imran Masood, Quality Specialist and Labs Head at Unilever – Dubai Personal Care Factory.
Unilever Maintains Full Control Over Its Quality Control Process With GlobalVision
Unilever products can be found in the homes of over 2.5 billion people worldwide in more than 190 countries. With hundreds of different products, Unilever brands have had a place in the day to day lives of consumers for over 90 years. With such a strong global presence, quality control is a top priority across the entire company. When consumers expect quality products, it is important to ensure that product packaging delivers on the brand promise.
Quality control that lives up to the company name
For Unilever Dubai, insight and innovation are at the heart of their business. It is essential for them to deliver brands and products that perform to the highest expectation of their customers, allowing for sustainable long-term growth across the entire company.
Specializing in personal care products like shampoos and lotions, any issues that arise in the quality control department must be immediately located and dealt with to ensure that products remain in line with the Unilever brand. The quality control department consists of a team of analysts who are responsible for performing all inspections and detecting any inconsistencies that can find their way onto labels and packaging. Any errors that are spotted must be immediately reported to the head of the department to ensure that only high-quality products are leaving the production facility.
Prior to implementing a digital quality control system, all proofreading was done manually in the lab by two proofreaders. With labels being visually inspected, it was often difficult to spot errors on small fonts that were printed in multiple foreign languages. Due to language barriers, one analyst would proofread Arabic text while another would proofread English text however, there were so many label variations that the analysts would often have to inspect artwork and labels in languages that they were unfamiliar with. This whole process quickly became difficult to manage and the company was struggling to get labels out quickly and efficiently. After opening up their Dubai plant in 2016, Unilever quickly realized that they would benefit from having an automated proofreading system like GlobalVision in place.
An end to proofreading inefficiency
After implementing GlobalVision Print Inspection in 2018, the process of inspecting incoming packaging materials improved tremendously. The system is primarily used to detect errors on incoming labels and packaging materials that they receive from their printers. Once the labels are received, they are placed onto bottles and other packaging containers. GlobalVision allows the quality analysts to compare the artwork on batches they receive from the printers against the approved artwork files developed by their graphics team. The software is then used to ensure that there are no discrepancies between the approved files and the finished products. According to Imran Masood, Quality Specialist and Labs Head at Unilever – Dubai Personal Care Factory, GlobalVision was selected over other proofreading software due to its ease of use, accuracy, and ability to help them save time along their quality control process.
“[GlobalVision] makes the entire process more streamlined and allows us to deal with foreign languages and very small font changes”
– Imran Masood, Quality Specialist and Labs Head at Unilever – Dubai Personal Care Factory
A complete solution
With manual proofreading, the quality department found it difficult to ensure 100% accuracy over the proofing process as human error was unavoidable. Having GlobalVision in place acts as a unit of control that allows the department to easily navigate inspections and ensure that no errors are leaving their lab. With over 200 labels to inspect per week, the cost and time savings are significant.
“Overall, the team is able to save between 10-15 minutes per label when proofreading with GVD.”
– Imran Masood, Quality Specialist and Labs Head at Unilever – Dubai Personal Care Factory
Due to the improved accuracy and overall increase in efficiency when it comes to inspections, the company can continue to focus on creating high-quality products that give consumers what they want for many more years to come.