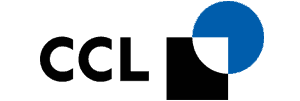
Download a PDF of the story.
CCL Label
Customer Story
By continuing, you agree to the processing of your personal data by GlobalVision as described in the Privacy Policy.
“The system is effective at finding almost every error possible. It’s one-hundred percent effective.”
Simon Lacroix, Quality Control Technician
GlobalVision Aces Test of Time Over at CCL Label
When CCL Label Montreal first started using GlobalVision, the pharmaceutical printing company had a good idea of what it was getting itself into with the automated QA software. Over 15 years later, it’s fair to say that CCL, having found success within an industry built primarily on the ability to catch mistakes, could not have been more right. It’s an assessment that is validated every single week like clockwork.
“Every week we challenge the equipment with a test, and we have samples with errors in it that we have to find,” says Quality Control Technician Simon Lacroix. “So far, it has never missed an error.”
Satisfied Customers
CCL has been taking advantage of GlobalVision systems since 2001 to inspect everything from leaflets and labels to literature in general. However, the company’s level of satisfaction isn’t measured just in time spent as a customer. It’s one of many factors.
“We catch critical errors once a month, sometimes more, but the critical errors we can find are maybe a letter that is erased or a missing dot. The system is effective at finding almost every error possible. One-hundred percent effective.”
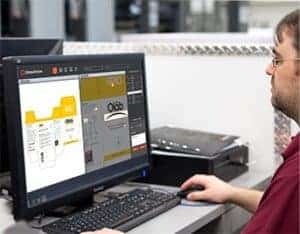
Graphics Inspection catches differences in a wide array of graphic files”. Excluding a separate GlobalVision counting tool, which Lacroix says can reduce the time spent on a given task by days,CCL has three separate systems spread throughout its plant. One inspects large-format sheets, another does smaller-format labels, and a third is dedicated to graphics.
It’s no exaggeration to say GlobalVision runs 24/7 at least in some capacity at CCL, with an estimated 40 to 50 inspections taking place a day making for approximately 10,000 each year. As such, GlobalVision must be doing something right.
“The demands of our customers is basically, ‘No errors.’ No errors at all,” reinforces Christine Houle, Head of Quality Assurance. “GlobalVision has helped us to become a reliable partner with our customers as well, along the supply chain. Customers come in for visits, and when they see the systems they leave here with more confidence in what we are doing.”
An Error-Free “GlobalVision”
With operations in 156 countries, CCL has no shortage of clients. There are also literally tons of plants all over the world, many of which have GlobalVision installed says Pierre Déry, the General Manager of the company’s Montreal facility. It’s all part of an ongoing standardization process.
“It happens sometimes that a job will be started here and could be completed by a sister plant somewhere. We want to make sure that everything is printed following the same procedures,” he says. “[Customers are] certain that, whatever the detection levels and sensitivity or system set-ups, the same set-ups will be used across the board.”
Déry is witnessing firsthand the benefits at just one plant. Primarily, its accuracy, which GlobalVision has proven to supply in spades.
“Second, it’s the lead time. When you’re producing millions of pieces, it takes time and, if you’re investing the time manually, it just doesn’t make sense. So, it accelerates a process from the proofing down to the actual product, because we are using the system from the beginning of the process to the end. That’s a big impact.”
At this point, there’s no going back.
“Trying to get rid of or not use an electronic verification system is absolutely out of the question. It’s impossible,” says Déry, specifically of GlobalVision.
In essence, it’s about moving forward instead. CCL is glad to continue to do just that with GlobalVision.