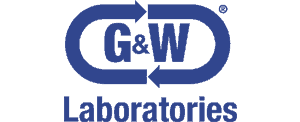
Download a PDF of the story.
G&W Laboratories
Customer Story
By continuing, you agree to the processing of your personal data by GlobalVision as described in the Privacy Policy.
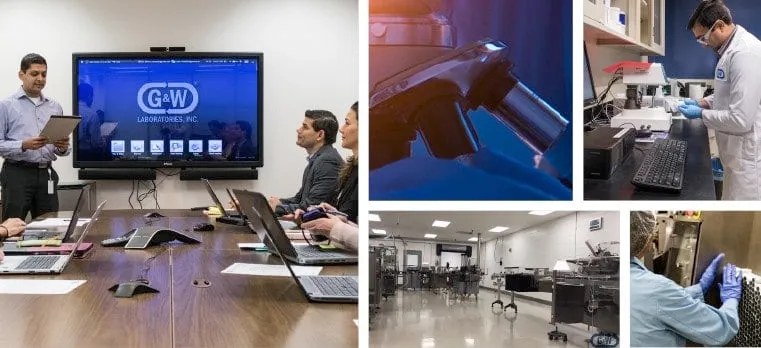
“If you look at [a document] long enough, you’re going to overlook something. So, [getting started with GlobalVision 20 years ago], we ensured the integrity of our product.”
Wanda Patton, QA Document Control Manager, G&W Laboratories
GlobalVision Upgrade Gives G&W New Appreciation for Automated Quality Control
From a proofreading perspective, it wasn’t long ago that G&W Laboratories was sent back to the 1990s. It was February 2017 when a legacy GlobalVision camera system they had been using since 1997 to help with their quality assurance finally broke down.
With no replacement parts unfortunately available anymore, the pharmaceutical company was forced back into the proofreading equivalent of the stone age. That was before they upgraded to the latest automated GlobalVision Print Inspection system.
“We would have a master and our sample that came in,” recalls Wanda Patton, the Quality Assurance Document Control Manager, of how things were two decades ago. “I would describe the graphics, the colors–as much as I could about the components, and they would read the text. Then we would switch. I would take the sample, and they would take the master and do exactly as I had just done. It was a totally manual, time-consuming process.”
Back to the Future of Quality Control
“We were back to 1996,” says Patton, who works out of the company’s North Carolina location. Patton oversees the QA department, but department titles blurred during the unscheduled trip back in time.
“It was a really big strain on the plant,” she says, adding production actually stopped several times because of the sudden switch back to manual proofreading. “We had chemists from the chemistry lab, with their degrees in chemistry and microbiology helping to read. We had people from the packaging department read. We reached out to all departments for help, and they all jumped in.”
“[We were asked] why we don’t have anything to run. Why can’t we get our inserts released? Where are our components? And then some of those people, instead of going home, would come back and help us proofread and then they understood. Nobody wants to read six-point font for six hours.”
Wanda Patton, Quality Assurance Document Control Manager, G&W Laboratories
Working with printed components such as tubes, cartons, labels, and patient leaflets, Patton foresaw things slowing down at the very least. The first leaflet she had to proofread manually again took six hours from start to finish.
“They would ask why don’t we have anything to run,” she reports. “Why can’t we get our inserts released? Where are our components? And then some of those people, instead of going home, would come back and help us proofread and then they understood. Nobody wants to read six-point font for six hours.”
Patton admits circumstances were less than ideal, as so few people can accomplish that very task effectively. Hence the need to not only go with GlobalVision the first time around but upgrade to an even faster system now.
Ensuring Integrity of Your Product
The previous camera system was a definite step up relative to manual proofreading as it enabled G&W to cut out the risk of human error.
“If you look at [a document] long enough, you are going to overlook something,” says Patton. “So, [getting started with GlobalVision 20 years ago] we ensured the integrity of our product.”
The difference is now, instead of potentially having to take multiple camera shots to inspect a leaflet and run several “mini inspections,” it’s just one pass through a scanner. What once took an hour and a half is now done in 15-20 minutes.
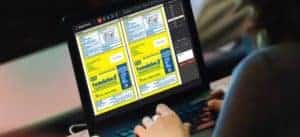
“I just can’t say enough good things about the improved turnaround time that we have on our components,” she reports. “Both the warehouse and production have been impacted positively because we’ve been able to get our things released and ready for production to stage for the line. There’s not so much a sense of urgency. Everything’s back to normal.”
The new, improved normal anyway. Patton is more than satisfied with the user-friendly system, GlobalVision support, and, most importantly, the reduction in testing release times. That’s not just relative to the manual process to be clear, but the previous camera system as well.
She calls essentially going straight from the aforementioned stone age to the latest automated GlobalVision system her “dinosaur to diamond experience.” She meanwhile likens upgrading from the previous GlobalVision camera system to going from a bicycle to an airplane. For G&W, it’s now the only way to travel. There’s no going back.