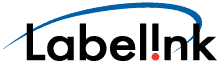
Download a PDF of the story.
Labelink
Customer Story
By continuing, you agree to the processing of your personal data by GlobalVision as described in the Privacy Policy.
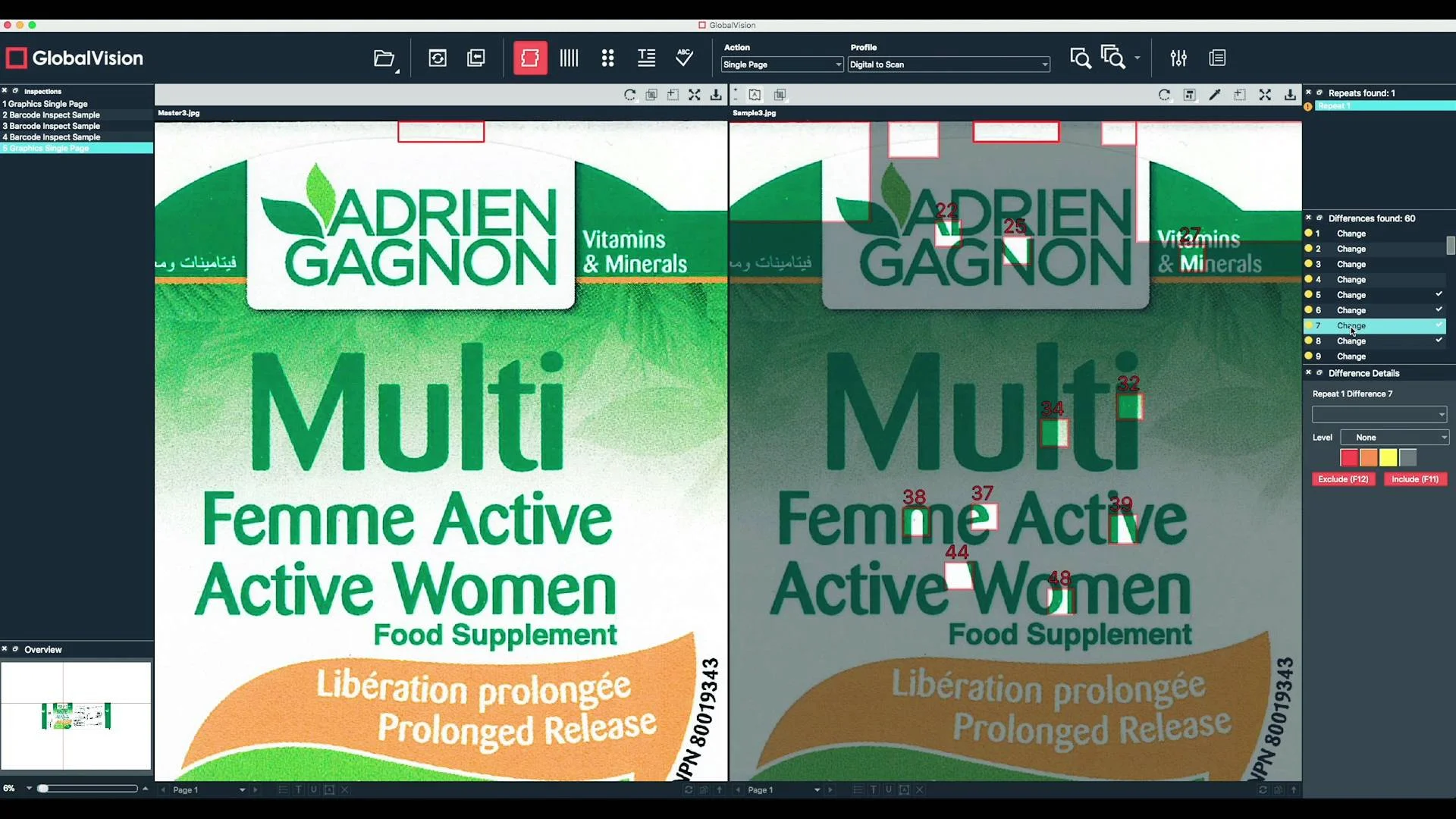
“It can be a period between two numbers. So, instead of 2.5 tablespoons, it becomes 25. So, regarding dosage, it becomes very complicated and dangerous, especially for a patient. Our video systems could not necessarily pick up on that point. Now [with GlobalVision], we can do it.”
Stephen Bouchard, President
GlobalVision Lives Up to Reputation as Labelink’s QC Platform of Choice
It didn’t take long for Labelink to discover the difference the GlobalVision automated proofreading platform can have on a company’s quality control process.
The Canadian print supplier has developed an expansive portfolio, featuring clients in everything from the food & beverage sector to the pharmaceutical industry. In business since 2004, Labelink only installed GlobalVision approximately a year ago. The change for the better has been dramatic.
“With one pharmaceutical client, we had six complaints about missing text or periods last year,” says Quality Supervisor Véronique Fortier. “This year, we’ve had none since we installed the software… Up to now, we’ve saved 30 production runs [overall], where there were missing periods. Thanks to the system, we were able to detect them in time.”
Checking Fine Print with a Fine-Tooth Comb
A missing character like a period may be small in size, but it can have a huge impact, especially in pharma. As such, eliminating errors is imperative to prevent their clients from having to issue market recalls, which is one of Labelink’s primary goals. President Stephen Bouchard calls GlobalVision an “insurance policy” in that regard.
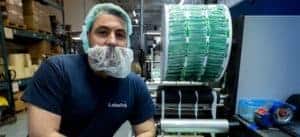
“It can be a period between two numbers. So, instead of 2.5 tablespoons, it becomes 25,” he says. “So, regarding dosage, it becomes very complicated and dangerous, especially for a patient. Our [old] video systems could not necessarily pick up on that point. Now [with GlobalVision], we can do it.”
The old system was long and arduous and required the use of a magnifying glass to help out with verifying the accuracy of fine print, just for starters. Bouchard, who came from the pharmaceutical industry himself and had heard of GlobalVision before, has no doubt the new process is a drastic improvement.
“It was a visual inspection with the help of an acetate [overlay],” he says of the old process. “We superimposed an acetate on the label to check if we missed anything. It became a manual visual inspection, where mistakes were possible especially when dealing with very small characters. Right now, [with GlobalVision] it’s automated and we’re sure not to miss anything.”
The “Most Complete” System
Labelink adopted GlobalVision in part at the behest of Fortier, who, herself, had experience with the platform at her previous company. She calls it the “most complete system” for inspections on the market as far as she knows, making the choice to switch to GlobalVision a relatively easy one when faced with alternative solutions.
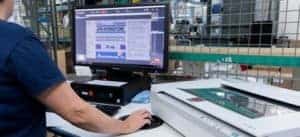
The familiarity with GlobalVision is a recurring theme at Labelink, especially now. Quality Control Coordinator Marie-Hélène Guitar, who had previous experience with GlobalVision as well, says it’s very easy to use from tester to tester.
The application’s versatility was also a selling point. Labelink initially sought out GlobalVision for its Print Inspection mode but decided to forego the purchase of expensive hardware in favor of its Barcode Inspection mode too. There haven’t been complaints regarding either since it was installed. Labelink is even looking to integrate it into their computer graphics system to better verify files during the preparation process.
“It’s a really efficient system,” says Guitar. “I don’t know of another one that covers all aspects of verification from printed labels to barcodes like GlobalVision.”