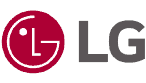
Download a PDF of the story.
LGE South Korea
Customer Story
By continuing, you agree to the processing of your personal data by GlobalVision as described in the Privacy Policy.
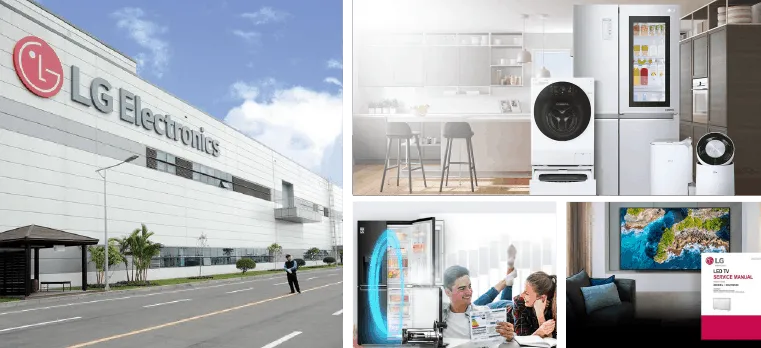
“We use GlobalVision in the verification and approval phase and our satisfaction is very high. Human errors and working hours have been reduced and the quality of our documents has improved”
Sujin Kim, Quality Senior Engineer, MD4 Team, Washing Machine Division H&A at LGE
LGE South Korea Implements GlobalVision in its Home Appliance & Air Solution Division
As a global technology innovation leader in the field of electronic products, mobile communication devices, and home appliances, LG Electronics currently conducts business in more than 140 countries around the world. In 2019, the company recorded sales of KRW 62,32 trillion. The company consists of five business divisions: Home Appliances & Air Solutions, Home Entertainment, Mobile Communications, Vehicle Component Solutions, and Business Solutions.
LG’s Home Appliance & Air Solution (H&A) division is a leader in smart home solutions, including robots and household appliances. Located in South Korea, they lead the market with innovative products that meet the needs of customers in various environments ranging from ultra-large buildings to industrial facilities.
The H&A department develops instruction manuals and caution labels for products around the world. The purpose of these manuals is to help customers use LG products safely, easily, and conveniently. Manuals include various product characteristics and information that helps users with any problems or troubleshooting. All instruction manuals are produced in one part with the possibility of applying additional information to batches of product manuals across the globe.
Difficulty with reworks
Once the contents of the manual have been modified, the H&A division would have to ensure that the new edits were correct compared to the existing content. Before implementing GlobalVision, the department was having difficulty verifying changes when comparing the before and after of text changes on PDF files. Visual inspections were often conducted, but it was difficult to locate changes that were accidentally made on images.
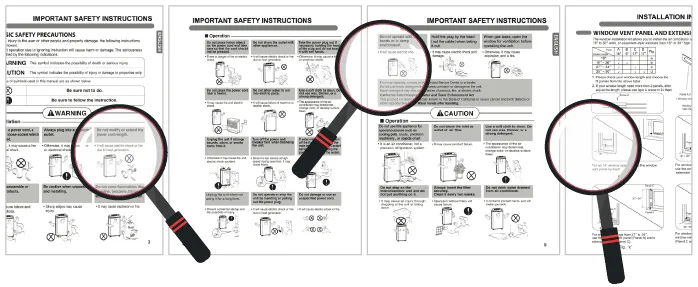
The H&A division had occurrences where an image change was made by the editing vendor on a page that was not requested. Although these types of errors are often made by the vendor, the final confirmation of manuals is the responsibility of the H&A division, therefore comparing version changes is necessary. “There were many situations in which parts other than what was requested were accidentally changed, but it was difficult to detect by visual inspection,” says Sujin Kim – Senior Engineer, MD4 Team, Washing Machine Division H&A. This led to the company experiencing rework issues multiple times a month, affecting the efficiency of their department and the quality of manuals for their customers.
The results with GlobalVision
GlobalVision was originally implemented in LGE South Korea’s incoming quality control department where it was very efficient at detecting deviations in images that may have been missed during visual inspections. While the defects can be corrected before the manuals get to customers, finding errors right before production still requires multiple reworks that can be long and inefficient. To improve this, the company decided to also implement GlobalVision at the digital file change stage.
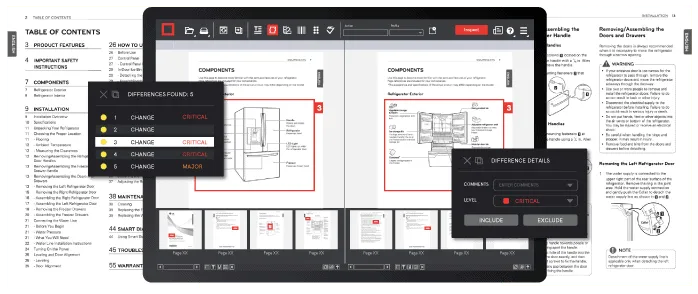
GlobalVision’s software is used when changes are made to the product documentation. The software enables the H&A division to eliminate manual inspections and accelerate approvals by attaching a comparison file before and after changes are made. Changes in content and images can easily be detected on all pages and can be quickly located due to the flashing of detected errors. Reports containing the found defects can then be shared across the department for quick review.
“We use GlobalVision in the verification and approval phase and our satisfaction is very high. Human errors and working hours have been reduced and the quality of our documents has improved” – Sujin Kim, Senior Engineer, MD4 Team, Washing Machine Division H&A at LGE.
The H&A division of LGE South Korea is also satisfied with the system, ease of use, and support received by GlobalVision.