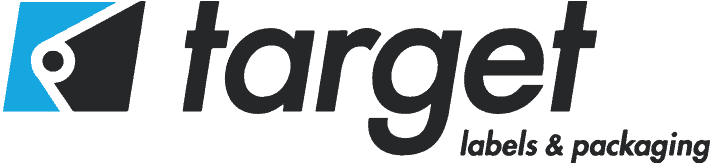
Download a PDF of the story.
Target Label
Customer Story
By continuing, you agree to the processing of your personal data by GlobalVision as described in the Privacy Policy.
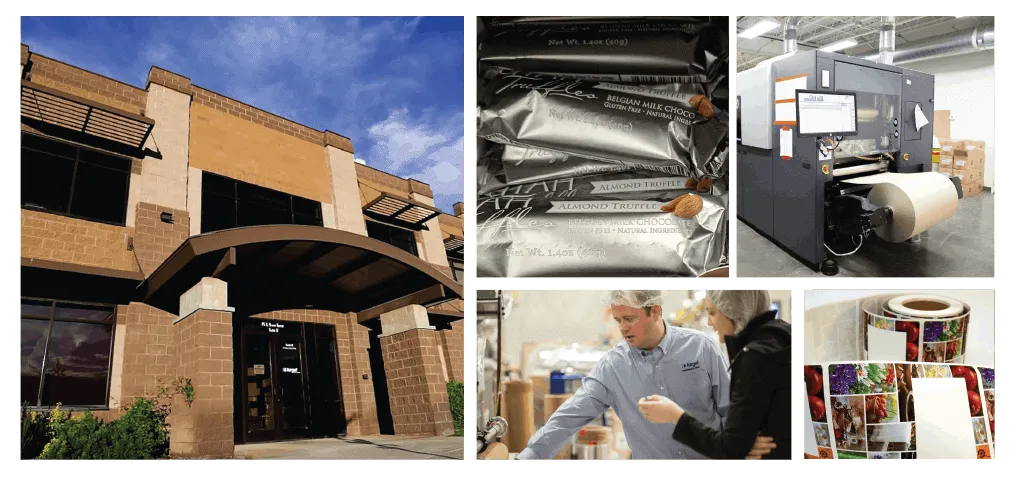
“Anyone looking to improve their process and be better in the area of quality control should consider implementing GlobalVision.”
Josh Jenks, Technical Sales Director, Target Label
Target Label takes a proactive approach to quality with GlobalVision
For Utah-based printing powerhouse Target Label, quality and growth have always been at the forefront of their business. Founded in 2006, this family-owned company began its journey printing pressure-sensitive labels before getting into flexible packaging in 2009. They then upgraded their entire facility to include state-of-the-art technology in 2013 and have been expanding their printing capabilities ever since, allowing them to experience significant annual growth over the past 13 years.
Today, Target Label prints labels and packaging materials for a variety of industries, primarily Food & Beverage, Nutraceuticals, and Pet Food. With a company goal of continuing to expand while maintaining a complete commitment to quality, Target Label recognizes that offering the latest in innovative print technology is a key factor when it comes to continuous growth.
Automated proofreading identifies gaps in the workflow
Before automating their quality control process, Target Label was primarily relying on the human eye to catch defects, causing the occasional error to slip by. According to Josh Jenks, Technical Sales Director at Target Label, the company incurred an error when someone in the graphics department put a customer’s logo on the wrong layer. The proof was then printed to match what they were producing instead of the master file the customer had signed off on. Unfortunately, the error went by undetected until it had been shipped, costing the company tens of thousands of dollars in products that were missing the customer’s logo.
According to Jenks, the majority of defects that slip by can be attributed to human error, especially since they outsource some of their prepress. By outsourcing parts of their prepress, the company loses some control over quality. There have been some occurrences where their prepress house had returned files that were not properly formatted, which then impacted the plate-making process. In other words, since their prepress house did not run a quality control check to find any registration issues, the plates were not properly created, causing alignment issues once the printing started. With files being touched at multiple stages by different departments, Target Label eventually decided to explore automation technology to reduce the risk of errors along their workflow.
More than a quality initiative with GlobalVision
In addition to optimizing their quality control process, Target Label saw GlobalVision as a powerful selling tool. Aside from catching critical errors, GlobalVision is a way for the company to show customers and potential customers that they are doing everything available to ensure that print jobs are done properly straight out of the gate. Having an automated proofreading system in place serves as a differentiator between Target Label and competitors as it shows that they are willing to spend money to ensure high-quality printing.
“[With GlobalVision], clients can get 100% of what they want every time, which is to prevent errors from happening. It is a proactive approach to quality versus a reactive approach to quality.”
Josh Jenks, Technical Sales Director, Target Label
After implementing GlobalVision, the company quickly realized that its benefits spanned multiple departments. On the very first day of using the system, the quality department was debating inspecting their digital items as errors on digital files were not very common. As it turned out, the very first job they inspected with GlobalVision led to them finding an error where a registered trademark was missing. This immediately gave them justification as to why they should use GlobalVision across the board rather than being selective on where to implement it.
The GlobalVision process
Today, GlobalVision is used in prepress at 2 stages. The initial check occurs when the first proof is prepared. The prepress operator will check the original artwork against the proof to ensure that there are no drastic changes. Once the proper edits have been made, they then move on to the second check. The second check is where the prepress operators step the approved file to get it ready for plates. They then take those proofs and compare them to the original stepped file. These checks allow the quality team to identify every touchpoint where files can change and eliminate any errors that could occur between stages.
Along with inspecting proofs against the original customer file and stepped files, Target Label also uses GlobalVision for quick comparisons such as reviewing artwork changes and grading barcodes. This helps cut costs and improve efficiency along the workflow as no one is sitting around manually looking for errors. It also gives them comfort in knowing that their plates are correct. After both inspections have been run, everything gets sent to the press for setup. They then go through with their normal approval process where they check color, content, registration, and print defects. Once that has been approved, they pull a repeat and scan it through the GlobalVision Print Inspection scanner to identify any hiccups that may have occurred. The results from the Print Inspection are communicated to QA, where they can act upon the differences found before printing the full job.
Aside from the ease of use of the system, Target Label appreciates the pixel-to-pixel accuracy of GlobalVision’s software. To Jenks, this is the most beneficial part of using an automated quality control platform. They also enjoy the reporting feature as it allows them to go back and review all issues before sending them to the customer, proving that they are indeed running quality inspections.
Continuous improvement and innovation support growth
As Target Label continues to grow, so do their requirements when it comes to quality and customer satisfaction. With GlobalVision, the company has been able to position itself as a leader in the areas of print quality and technology by offering a safety net for any unintended errors on their files. As Jenks states, anyone looking to improve their process and be better in the area of quality control should consider implementing GlobalVision as it forces them to look at quality differently.
“There’s only so much you can do without adding something like GlobalVision to improve your quality department. GlobalVision makes it so that you have to step outside your comfort zone in order to improve your quality process.”
Josh Jenks, Technical Sales Director, Target Label