More than in any other sector, pristine packaging is critical to ensuring success in the pharmaceutical industry.
Aside from being visually appealing, packaging must be free from the five most common critical mistakes that often plague the pharmaceutical industry. Read on to see which mistakes these are and how you can avoid them in your packaging processes.
Mistake #1: Inaccurate Braille
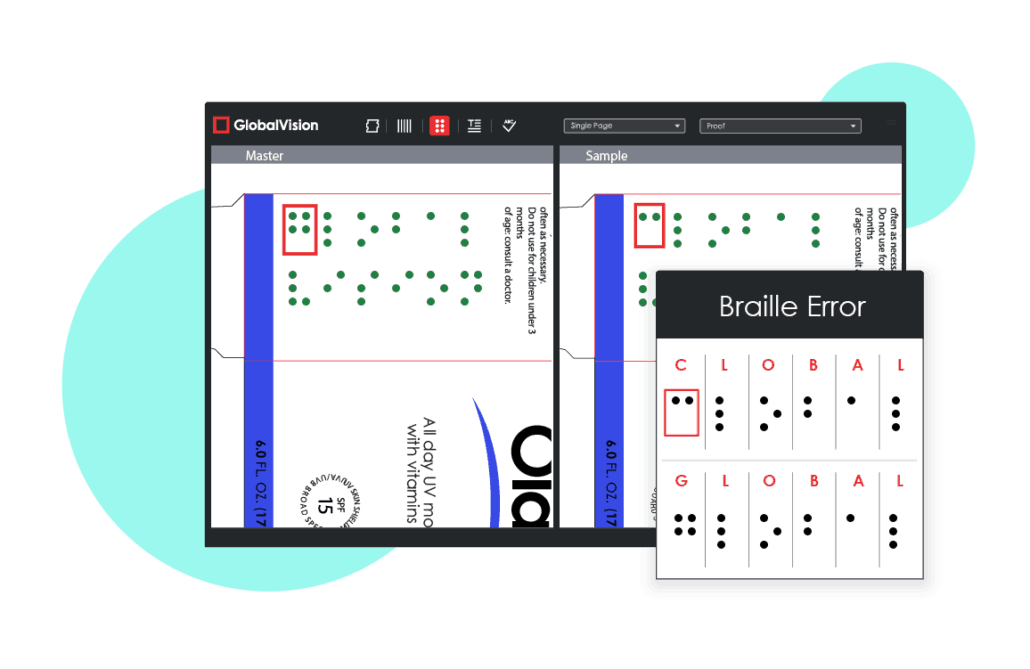
The importance of braille is often difficult to grasp by those who are not visually impaired. Despite there being no legal requirements for braille on pharmaceutical packaging in the United States, braille accuracy must still be ensured and not taken for granted.
Traditionally, braille on pharmaceutical packaging has been difficult to proofread, causing errors to be quite common.
Compared to European nations that have strong legal requirements for braille, North America’s International Association of Diecutting and Die Making (IADD) Can-Am Braille Standards are viewed as more like requirements. As a result, braille is not a high priority for pharmaceutical companies operating solely in the United States, causing its accuracy to oftentimes suffer when it does appear on packaging.
Mistake #2: Translation Mistakes
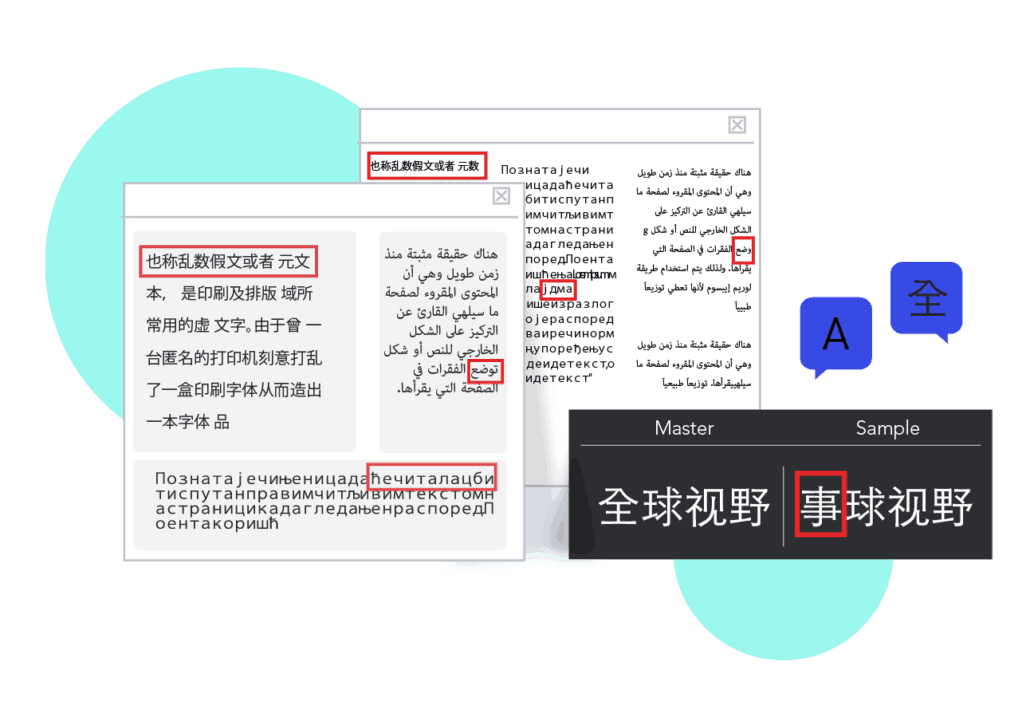
There is an inherent risk that something will get lost in translation when a pharmaceutical company opts to sell its products in a foreign market.
Packaging content is often translated through a third-party company that may lack proper context, resulting in translation errors. Once the text is sent back to the pharma company, it may have to be proofread again for that very same reason.
Theoretically, the proofing could also be done in-house by an employee who speaks the language in question. However, they could end up performing quality assurance checks on top of their regular duties, which could be in a completely different department. They may not specialize in writing or translation, meaning mistakes can make it to market as a result.
Mistake #3: Failure to Comply with Regulations
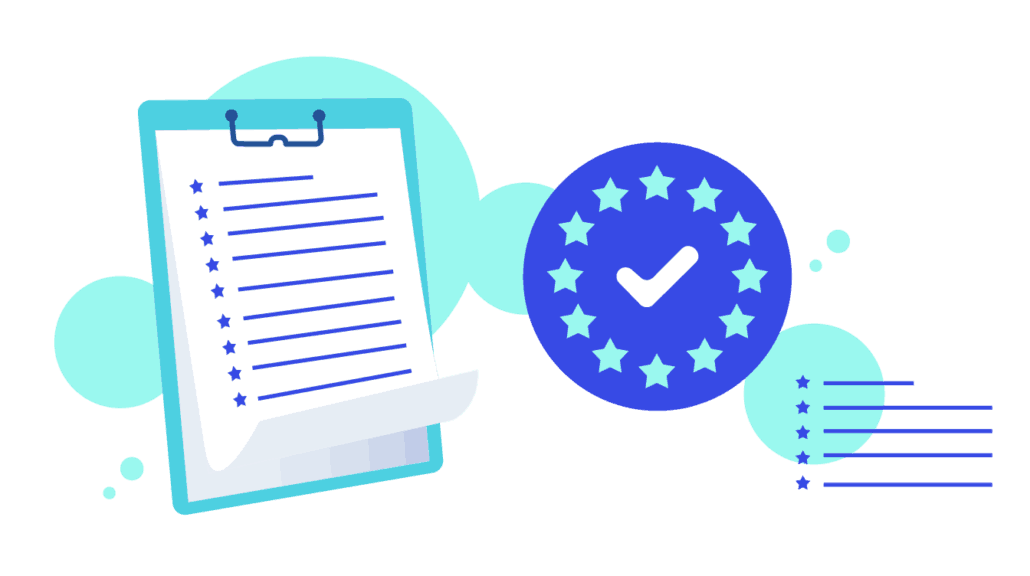
As companies dive into new markets, they expose themselves to risk in regard to translations and potentially drastic regulatory differences. Pharmaceutical manufacturers go to great lengths to ensure compliance with regulations, so much so that they have entire departments dedicated to compliance.
There is also a specific set of official packaging and labeling guidelines in 21 Code of Federal Regulations Part 211 (when dealing in the United States, for example). These range in subject matter from the displayed expiry date to the use of appropriate equipment to examine packaging for mistakes.
One key piece of information that illustrates how easy it is for mistakes to be made when it comes to quality control: pharma companies are not only responsible for ensuring they follow GMP (Good Manufacturing Practices) in-house with regard to artwork, packaging, and labeling. They are also responsible for the product itself, and therefore their distributors and suppliers too.
Mistake #4: Packaging Inconsistencies Due to Printing Issues
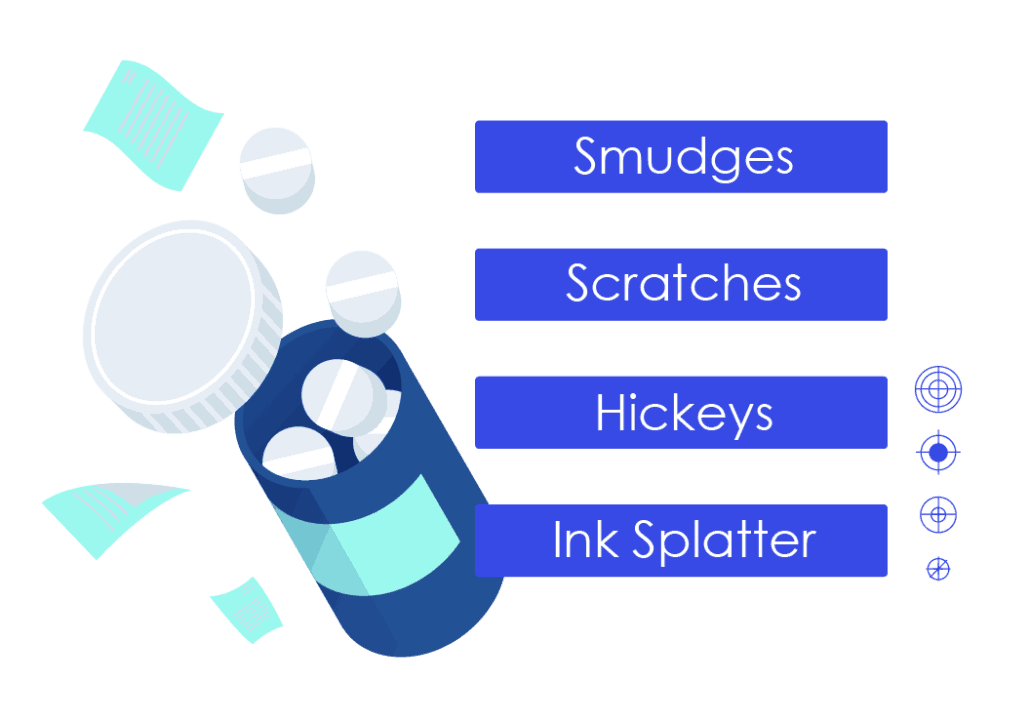
Problems with the printing process and print suppliers can lead to a variety of relatively minor issues that add up. A slightly off shade of color, the use of a different font, distorted artwork, and even a simple blemish could be enough to damage brand equity.
Quality issues such as these reflect badly on the quality of the product itself, and may even lead to costly recalls if significant enough.
Mistake #5: Typos, Typos, Typos
It is oftentimes the smallest mistake that has the largest impact (and not in a good way).
Even if the branding is noticeably off (see packaging inconsistencies above), consumers will likely still buy the medication they need. In that sense, it is the functionality of pharmaceutical packaging that dictates successes and failures. The information on a carton is of utmost importance, which is why it is imperative that there be no typos whatsoever.
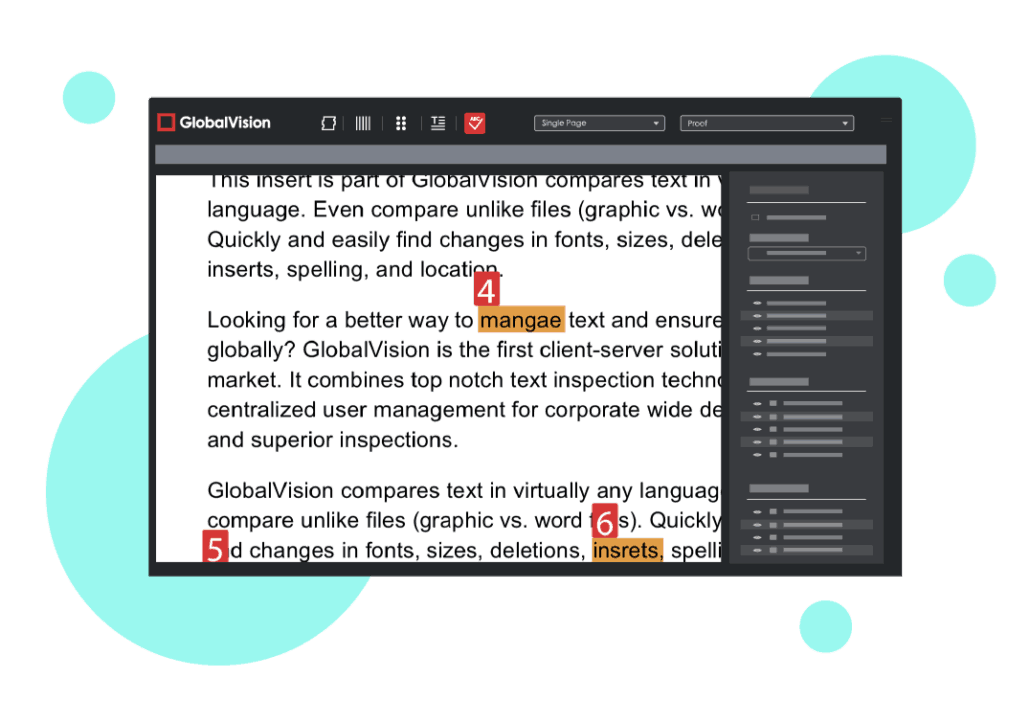
Companies should hope mistakes do get caught before a sale is made due to potential health ramifications to consumers in the event that dosage information is misprinted. A misplaced decimal is enough to have severe consequences. In such an instance, regardless of how successfully drug packaging markets and sells the product, the brand itself will face an uphill battle in recovering financially.
Pharmaceutical companies still make easily avoidable mistakes, even with the knowledge that simple typos can cause as much damage as they do.
In regards to the latest drug recalls by the FDA, labeling mistakes are the most common reason from a packaging perspective, which serves to underscore the need for pharma companies to get it right and up their proofreading process. Failure to do so and they will find sales and stock prices going down in a hurry instead.
Eliminate Mistakes in Packaging For Good
While the visual appeal of any product packaging is important, avoiding common errors and mistakes in packaging is even more crucial.
Packaging inconsistencies due to printing problems and, most notably, typos, can lead to major health risks and financial setbacks as the long list of past FDA drug recalls have emphasized and shown us.
Pharmaceutical companies must prioritize quality control, proofreading, and adherence to regulations to maintain their reputation and safeguard the well-being of consumers. In this industry, it's not just about what's inside the package but also how it is presented and communicated to the world. In an industry where there’s little to no room for error, setting up proper proofreading processes is of critical importance.
Ready to step into the world of automated quality control? Learn more about our innovative proofreading software and discover how this technology can transform your daily business operations.
Get more from GlobalVision by checking out these additional resources:
The 5 Most Common Printed Packaging Errors Guide
Misconceptions of Packaging Quality Control
Learn Why Error-Free Packaging and Labeling are a Must
Get your Complete Guide to Meeting FDA Labeling Requirements Here
Learn How Some of the World’s top Pharma Companies have Cracked the Efficiency Code with Automation
Related GlobalVision Services: