In the UK healthcare industry, medicine packaging plays a crucial role in ensuring the efficacy and security of not only medical products but of consumers as well.
Over the years, requirements of UK medicine packaging have undergone significant changes, driven by advancements in technology, changes in consumer expectations and needs, and, most importantly, the ever-evolving stringent regulations imposed by regulatory agencies such as the MHRA.
Understanding and navigating these regulations is essential for medical companies to bring their products to market quickly and securely, and for healthcare professionals to ensure patient safety when prescribing medicine.
The Early Days of UK Medicine Packaging
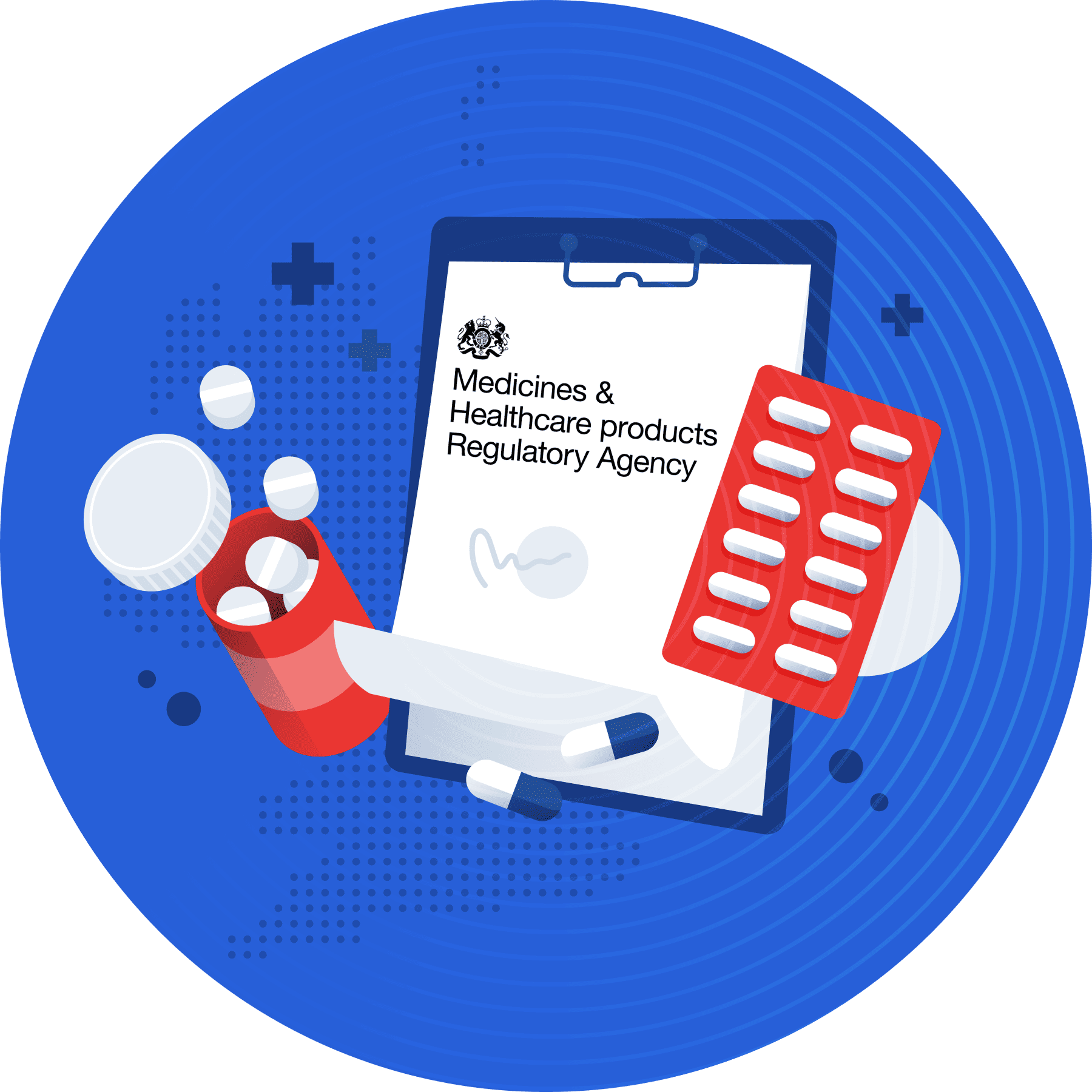
Throughout history, the main role of UK medicine packaging has been to safeguard and conserve the contents of medical products. Glass bottles and vials were commonly used and were typically sealed with cork stoppers.
These bottles were usually accompanied by simple labels containing essential information. The labels were essentially handwritten instructions and information on paper that would be wrapped around the bottle. Overall, packaging was basic, serving the primary purpose of protecting the medication from external contaminants.
However, as the medical industry advanced, so did the need for standardized and regulated packaging to ensure patient safety and facilitate the administration of medications.
Blister Packs and Pill Bottles
As medicine research advanced, so did the need for more sophisticated packaging. In the mid-20th century, blister packs, the ones we so often see today, emerged as a popular choice. This sealed, foil-based packaging, offered enhanced protection against moisture and air and helped in extending the shelf life of medications.
Glass bottles were becoming less common as plastic pill bottles became a more popular substitute. They provided a more user-friendly and portable alternative to the old, heavy, and fragile glass bottle.
The Rise of Regulation in UK Medicine Packaging
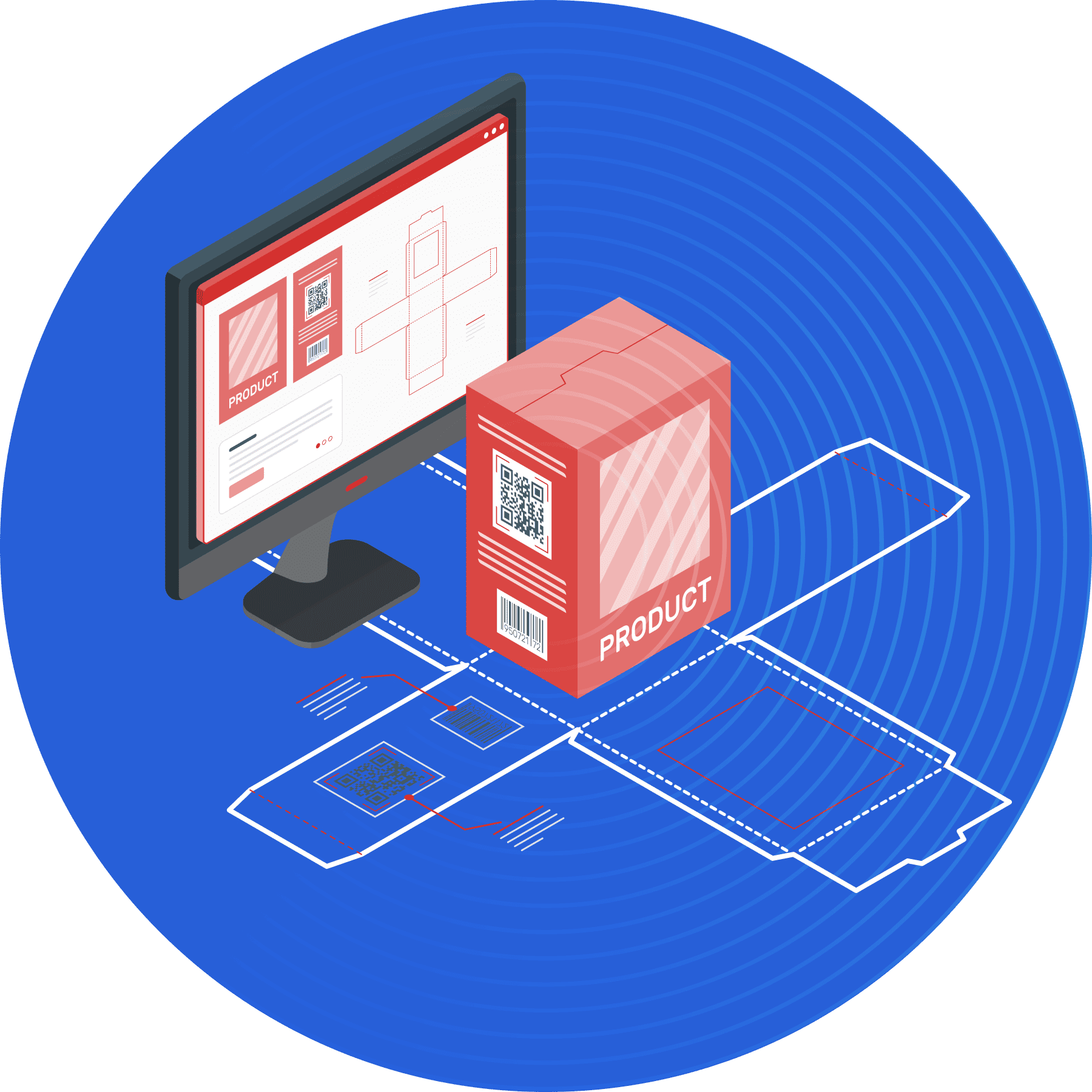
While advancements in UK medicine packaging were present throughout the 20th century, the greatest turning point came with the strict implementation of medicine regulations aimed at standardizing the industry. This was due to the fact that traditional UK medicine packaging and the lack of proper guidance and regulation were proving to be greatly limited in ensuring the safety of products and consumers.
Regulatory agencies have been present globally since the beginning of the 20th century, but in the UK, the Medicines and Healthcare products Regulatory Agency (MHRA) has been at the forefront of setting guidelines to ensure the quality, safety, and efficacy of medical products since 2003.
Their main responsibilities include:
- Ensure safe and effective medicines, medical devices, and blood components
- Establish a secure supply chain for healthcare products
- Promote global standardization for the safety and effectiveness of biological medicines
- Educate the public and healthcare professionals on the risks and benefits of healthcare products for safer use
- Support innovation and research for public health benefits
- Collaborate with UK and international partners for early access to safe healthcare products and to safeguard public health
Since its implementation, the United Kingdom has played a pivotal role in shaping the evolution of UK medicine packaging through its stringent regulatory framework. The MHRA consistently sets forth updated guidelines that govern the packaging of medicine, ensuring safety, efficacy, and adherence to quality standards.
Labeling Requirements of UK Medicine Packaging
UK medicine packaging is made up of many different components that are all strictly regulated and controlled to ensure its accuracy and safety for use and consumption.
One of the most critical aspects of UK medicine packaging is the labeling, or the information provided on labels. Regulations mandate that packaging must include essential details such as the name of the medicine, dosage instructions, expiry date, batch number, and manufacturer information, to name a few.
Additionally, UK medicine packaging labels often feature critical safety information, such as potential side effects and storage guidelines. The main goal of a label is to ensure that individuals administering or consuming the medication are well-informed about its proper use and potential risks.
Compliance with labeling regulations not only supports the safe and effective use of medicines but also plays a pivotal role in promoting transparency and accountability within the medical industry. Strict adherence to labeling requirements contributes to the overall goal of ensuring public health by providing users with all the necessary information and knowledge needed to make informed decisions about their healthcare.
Tamper-Evident Measures
Tamper-evident packaging is described as “having one or more indicators or barriers to entry which, if breached or missing, can reasonably be expected to provide visible evidence to consumers that tampering has occurred.”
These measures in UK medicine packaging play a crucial role in ensuring the safety and integrity of medical products. The measures are implemented to provide visible signs of interference, making it evident if a package has been tampered with or compromised.
Common tamper-evident features include seals or bands that are broken or altered when the packaging has been opened. By incorporating these features and measures, UK medicine packaging manufacturers aim to protect consumers from potential tampering, contamination, or unauthorized access to medications.
Tamper-evident packaging not only serves as an added layer of protection and security but it also builds trust among patients and healthcare professionals, assuring them of the authenticity and safety of the medicine inside a package. This added security measure contributes significantly to maintaining the quality and reliability of medicine products throughout the supply chain, ultimately safeguarding public health.
Child-Resistant Packaging
Another important addition to UK medicine packaging regulations came in the later half of the 20th century. Child-resistant packaging became a requirement, addressing concerns about accidental ingestions and poisoning of young children. This type of packaging is designed to be difficult for children under the age of five to open, thus reducing the likelihood of unintentional ingestion.
Child-resistant UK medicine packaging was first introduced into the United Kingdom in the mid 1970s but only became standardized in 2001. Since then, a number of different regulations have been put in place, including European and International standards, as well as the Human Medicines Regulations 2012 and GHS/CLP, which became fully effective in 2015.
Since its introduction, child-resistant packaging has undergone many changes, not only in increasing resistance to potentially being opened by children but also in optimizing usability for adults. There have been continuous efforts to increase the safety of these products and their packaging with constant new developments in packaging improvements.
Barcoding and Serialization
Barcoding and serialization are integral components of modern UK medicine packaging, designed to enhance traceability, authenticity, and overall supply chain security.
Barcoding involves the assignment of unique identifiers, typically in the form of barcodes, to individual medicine packages. This unique identification enables efficient inventory management, reduces errors in product distribution, and facilitates rapid tracking throughout the supply chain.
Serialization takes this a step further by assigning a distinct serial number to each medicine unit, allowing for precise tracing of products from manufacturing to distribution to the end-user. These measures not only contribute to streamlined logistics but also play a pivotal role in combating counterfeit medicine and in ensuring patient safety.
GMP (Good Manufacturing Practices)
Good Manufacturing Practices (GMP) in UK medicine packaging represent a set of strict quality standards and guidelines that medicine manufacturers must adhere to in the production of packaging materials and systems.
GMP regulations ensure that the entire product lifecycle, from development and production to labeling and storage, follows specific protocols aimed at consistently delivering safe and high-quality UK medicine packaging.
Compliance with GMP standards is crucial for maintaining the integrity of medicines and preventing contamination or defects in the packaging. These practices encompass various aspects, including personnel training, hygiene, documentation, and equipment calibration.
By adhering to GMP in UK medicine packaging, manufacturers uphold the highest standards of quality assurance, contributing to the safety and efficacy of medical products and reinforcing the trust of healthcare professionals and consumers in the integrity of the overall medicine supply chain.
Environmental Sustainability
In recent years, there has been a growing emphasis on environmental sustainability in UK medicine packaging. Regulatory agencies are encouraging medical companies to adopt eco-friendly packaging solutions, reducing the environmental impact of the industry.
Manufacturers increasingly focus on adopting eco-friendly practices and materials to minimize their carbon footprint. This includes exploring recyclable, biodegradable, or compostable packaging options and optimizing packaging designs to reduce material usage.
Additionally, efforts are being made to enhance energy efficiency in the production processes and choose environmentally responsible printing inks and coatings. The aim is to strike a balance between ensuring the safety and efficacy of medical products while minimizing the environmental impact associated with their packaging.
By embracing sustainable practices, the medical industry not only aligns itself with global environmental goals but also responds to the growing demand from environmentally conscious consumers.
Smart Packaging and Technological Integration
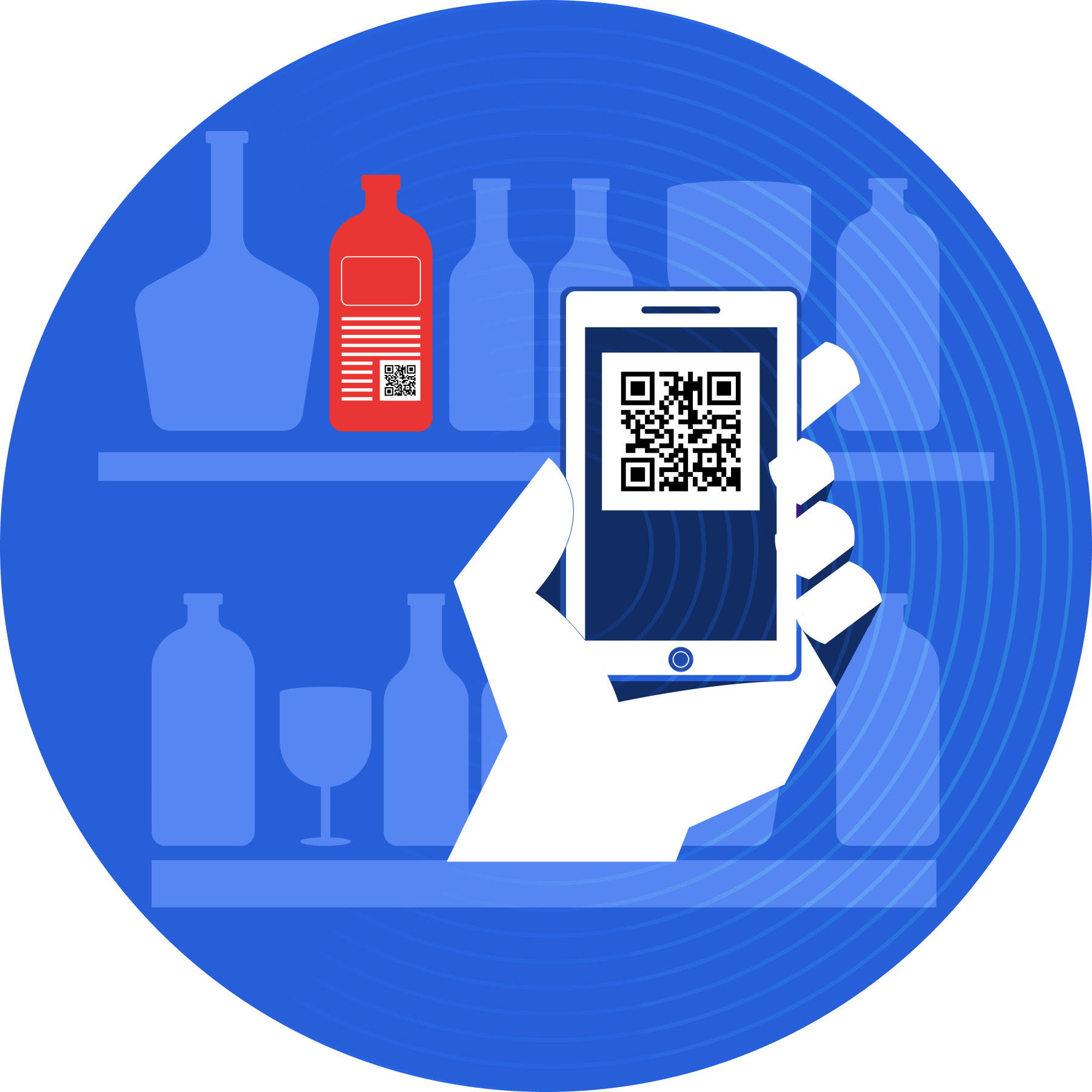
UK medicine packaging in the 21st century vastly differs from the packaging used over a hundred years ago. In recent years, technological advancements have revolutionized UK medicine packaging, with smart packaging becoming the newest trend in the industry.
This packaging is equipped with features like temperature monitoring, NFC (Near Field Communication) tags, QR codes, and interactive labels. These innovations not only ensure the integrity of the medication but also empower patients with information and enhance overall healthcare management.
Innovation in UK Medicine Packaging - Automated Proofreading
As the accuracy of all packaging content is of extreme importance, technological solutions that ensure packaging integrity are also increasing in popularity. Automated proofreading is one of those innovative solutions in UK medicine packaging. Automated proofreading aids in maintaining packaging accuracy by inspecting all types of regulatory content that would be present on UK medicine packaging. It helps companies uphold packaging and manufacturing standards with greater ease and efficiency, ensuring compliance with UK medicine standards and beyond. This technological innovation provides better proofreading results and enables higher-quality UK medicine packaging as it acts as an added layer of security in quality assurance processes. In essence, automated proofreading works by comparing two documents to find discrepancies between the two. The innovative software conducts comprehensive inspections and proofreads all packaging assets from text, color, graphics, barcodes, braille, and more. Through automated proofreading, inspections of packaging components are completed exponentially faster than traditional proofreading, and a task that once took hours or days to complete is now reduced to only a few minutes.
Benefits of Automated Proofreading
Automated proofreading plays a crucial role in enhancing the quality and compliance of UK medicine packaging. Some ways in which automated proofreading helps in UK medicine packaging includes:
- Error Detection: Automated proofreading quickly detects all potential errors on UK medicine packaging, ensuring the complete accuracy and quality of a product. This is not only important for regulatory compliance, it is also crucial for patient safety, as clear and error-free packaging guarantees critical medicine information such as ingredients, dosages, expiry dates, etc., are being accurately portrayed, preventing potential life-threatening consequences and ensuring patient and user health.
- Consistency Checking: Automated proofreading can verify consistency in terms of terminology, dosage information, and instructions across different sections of the packaging. Consistent information helps prevent confusion among healthcare professionals and patients.
- Regulatory Compliance: UK medicine packaging must adhere to strict regulatory requirements, including specific language and formatting. Automated proofreading helps ensure that the packaging content complies with these regulations, reducing the risk of non-compliance issues, including fines, product recalls, and legal actions.
- Efficiency and Speed: Automated proofreading significantly speeds up the proofreading process compared to manual methods. This efficiency is particularly beneficial in the fast-paced pharmaceutical industry, where accurate and timely product releases are critical.
- Version Control: Automated proofreading tools can help manage version control, ensuring that the correct and most up-to-date information is included on UK medicine packaging. This is crucial for avoiding mistakes associated with outdated content.
- Consistent Branding: For medical companies with multiple products, maintaining consistent branding across packaging materials is essential for brand recognition and trust. Automated proofreading tools contribute to ensuring this consistency.
By leveraging automated proofreading in medicine packaging, companies in the industry can improve the overall accuracy, quality, and compliance of their packaging. This not only increases patient safety but also helps maintain the integrity of medical products.
Customer Case Study: Automated Proofreading For Error-Free Medicine Packaging
Prior to implementing GlobalVision, all materials at Bristol-Myers Squibb (BMS) Shanghai were manually reviewed by their Quality Control department. Manually proofreading each packaging component often took too long and was too reliant on the SASS Project Manager. As they only relied on the human eye to catch errors, the risk of faulty inspections was high.
For a major pharmaceutical company such as BMS, letting a critical packaging error slip by could have damaging effects on its reputation. It may also result in reprints or recalls which can impose huge costs on the business. Worse, it can cause potential consumer harm if these packaging errors made it to market.
The BMS Quality Control Department uses GlobalVision to inspect incoming packaging materials such as cartons. Batch by batch, the packaging is compared to the approved samples to catch any differences between the two. As a result of the automation, the Quality Control Department has found that its revisions could be completed faster and more effectively.
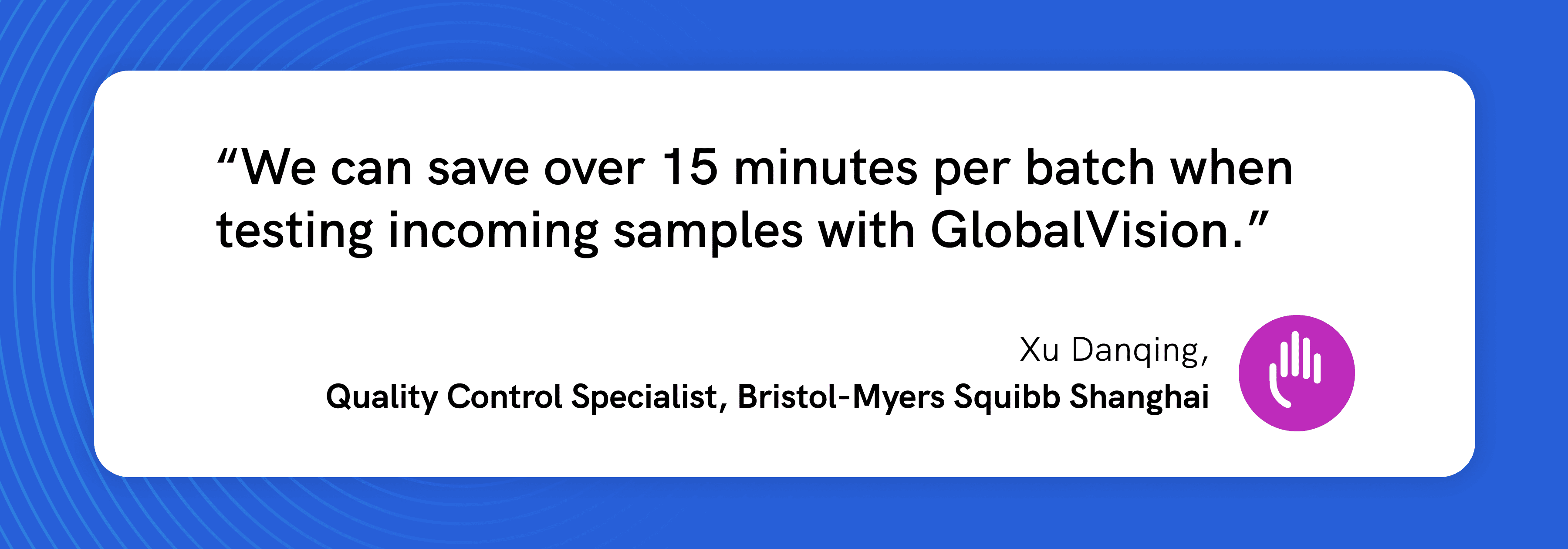
Through the implementation of GlobalVision, BMS Shanghai increased its level of efficiency and accuracy, further aligning its commitment to quality when it comes to both packaging and patients.
The Future of UK Medicine Packaging
The transformation of UK medicine packaging throughout the years has been shaped by dynamic factors such as evolving regulations, changing consumer needs, technological advancements, and a heightened emphasis on safety and responsibility.
The industry, from basic glass bottles to cutting-edge smart packaging, has consistently adapted to meet contemporary demands, with the MHRA playing a pivotal role in maintaining and enhancing these standards.
Each advancement in the industry shows a commitment to ensuring the highest quality and safety standards. Notably, the integration of technological solutions, including automated proofreading tools, emphasizes this commitment by improving accuracy and safeguarding packaging and, by default, healthcare professionals and consumers alike.
Automated proofreading serves as a comprehensive solution that not only streamlines quality assurance processes but also facilitates accuracy and compliance for UK medicine packaging manufacturers and beyond.
To experience the transformative power of automated proofreading, request a demo of our innovative software and witness firsthand how this technology can revolutionize your daily business practices.