Terms like “audit” and “inspection” are prevalent in any manufacturing business. The first one refers to analyzing manufacturing organizations and processes, whereas the second refers to any product-checking activity.
Generally, quality inspectors do this by following a pre-established list based on certain product specifications. In fact, any type of product can be inspected, starting with just the components used for the product to semi-finished ones and (most often) the finished product itself.
According to the ISO 2859 standard – which is derived from MIL-STD 105 E – quality inspection involves activities such as testing, gauging, examining, or measuring one or more product characteristics.
However, inspection efforts end when the results are compared with specified requirements to determine whether the inspected characteristic achieves conformity.
Why Early Quality Inspections Are Better
This is a crucial concept for any product developer because in the manufacturing world, the sooner we identify and eliminate errors, the better.
It all follows the 1:10:100 ratio, but before jumping to that, let’s remember that there are only six paths on which we can deal with errors. First, they fall into three categories: development, production, and delivery. Then, once identified, all we can do is either prevent or correct them.
Identifying and correcting an error in production will likely cost you 10 times more
(in both time and money)
According to multiple studies, there is a 1:10:100 cost/time ratio between these three broad categories. In other words, identifying and correcting an error in production will likely cost you 10 times more (in both time and money) than it would in development. Following the same ratio, an error will then cost you 100 times more to fix if it actually reaches the consumers.
That’s why applying quality inspection only at the end of the production line is a very risky move that only a few major companies dare to take. Big, organized, and customer-oriented companies are now focusing on inspecting earlier to save resources.
The Importance of Quality Inspection in Print
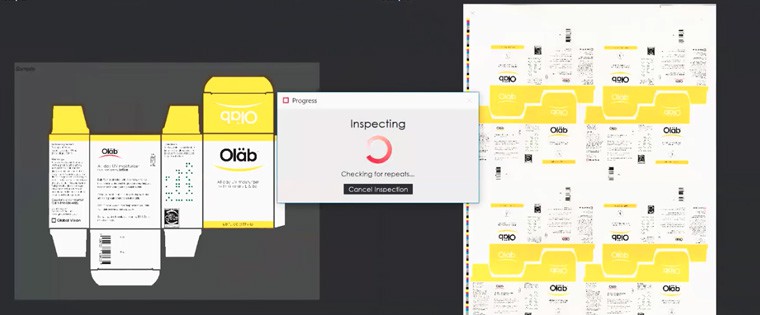
Companies needing to print in bulk will find that having a quality inspection process in place is extremely beneficial.
Print inspection systems can provide the assurance and quality control your company needs to minimize mistakes. They will also guarantee the delivery of consistent results that will enhance your brand’s image through error reduction.
In fact, the role of quality inspection systems becomes even more vital when dealing with offset commercial printers. Given that most printing presses operate at incredibly high speeds, irregularities in the final product are more than possible, if not mandatory. Quality inspection software in print – as opposed to manual inspection systems – provides the necessary accuracy to achieve consistent and flawless results on a regular basis.
Modern Print Inspection
Modern print inspection systems consist of advanced technology that links with your printing press or web rewinder to achieve exceptional results. It works by integrating vision systems (cameras), web viewers, and high-tech software that will catch any errors in time before they are printed in bulk.
Over the years, these quality inspection systems have been developing at a rapid pace. Nowadays, you can find multiple options online at very competitive prices. In fact, given that they require little to no maintenance, one of the key advantages of implementing these non-traditional tools is that you only need to make a one-time investment.
Other benefits include ease of use and operation and the ability to have more control over your result.
Conclusion
Quality inspection is an essential part of every production line.
Those who don’t understand how valuable it is are not looking at the big picture. Money-wise, the cost of manufacturing a product extends far beyond the build cost, as it continues across its lifecycle, from support and delivery to warranty claims and – for some products – disposal.
It might seem like an unnecessary investment now but, with proper management, they can reduce future costs, relating to customer support, warranty returns, and rejected/returned items. They can even add value to your company, as you’ll count on a competitive defense tool that will eventually pour more money into your pockets.
SECURING THE BRAND PACKAGING WORKFLOW
Read our white paper on how to automate printed packaging quality
control and the different techniques and systems that can be used in the packaging workflow.